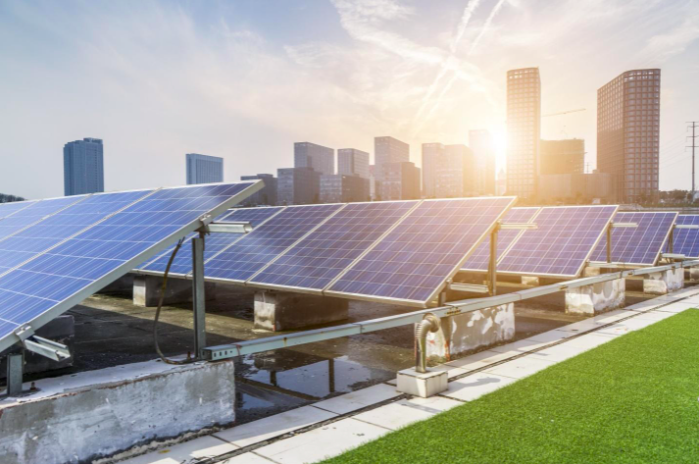
What the Solar Panel Manufacturing Process Actually Looks Like
Did you know that the first solar panel or solar cell was created in the 1800s?
Edmond Becquerel discovered the photovoltaic (PV) effect way back in 1839. But it was Charles Fritts from New York who created the first working solar cell in 1883. It was a selenium solar cell with an energy conversion rate of a mere 1 to 2 percent!
Well, you’ve got to start somewhere, right?
Today, solar panel manufacturing produces cells with an energy efficiency rating of 11 to 15 percent. While the number still seems low, they can generate enough electricity to cover most residential and commercial needs.
How does a solar panel company produce photovoltaic cells anyway? Let’s look at how the solar panel industry manufactures the panels you see on top of homes today.
Solar Panel Manufacturing Starts With Silicon
Silicon is the building block of solar cells, which is fortunate because it’s the second most abundant element on Earth. Silicon is a semiconductor material that exhibits a photovoltaic effect. It means that it can absorb energy from sunlight and convert it to electricity.
The solar panel industry uses sand as the raw material for silicon. A high-temperature furnace then turns the collected silicon into ingots.
A wire saw slices the ingots into precise, thin discs called wafers. These will get treated with a reflective coating. The wafers, together with metal conductors, make up a solar cell.
Monocrystalline vs. Polycrystalline vs. Thin-Film
Not all solar cells are created equal. What differentiates mono and polycrystalline cells is whether they’re made from a single silicon crystal or many.
Monocrystalline cells are the most efficient because they’re the “purest,” created from a single silicon source. If you want the best of the best, these are the ones to get. Find out more at https://blueravensolar.com/missouri/.
Polycrystalline cells are somewhat less efficient than monocrystalline. On the other hand, thin-film panels use photovoltaic material laminated onto a surface like glass. Thin-film production is cheaper, but it sacrifices durability, and the panels are also the least efficient.
Putting Solar Cells Together to Make a Panel
The next step is to solder a bunch of solar cells together to form one solar panel. For reference, the standard size for residential use is a 60-cell panel. Large-scale installations use 72-cell panels.
The collection of cells will need protection from all sides. A thin layer of glass protects the front, while a durable, polymer-based material shields the back.
A metal frame fuses all the layers and protects the panel from impact and weather. The structure also allows the securing of the solar panels on rooftops with a mounting system.
Testing for Quality
The last step before shipping them out is to test the panels for quality. The quality control team searches for any defects, such as cracks or bends. If they find any, they’ll discard the defective panels.
The panels also go through rigorous testing to evaluate their efficiency. Another vital aspect of the testing process is to ensure that the structure can hold up to harsh weather conditions.
Wrapping Up
Solar panel manufacturing has come a long way from the time of Charles Fritts and his first solar cell. The technology also keeps improving, and we can expect higher efficiency solar panels in the future. Good news for us and our planet!
For more tech news, please feel free to browse our site.